Trade press, 2014-05-28, 12:00 am
Expanded metal made from ultra-thin tinplate
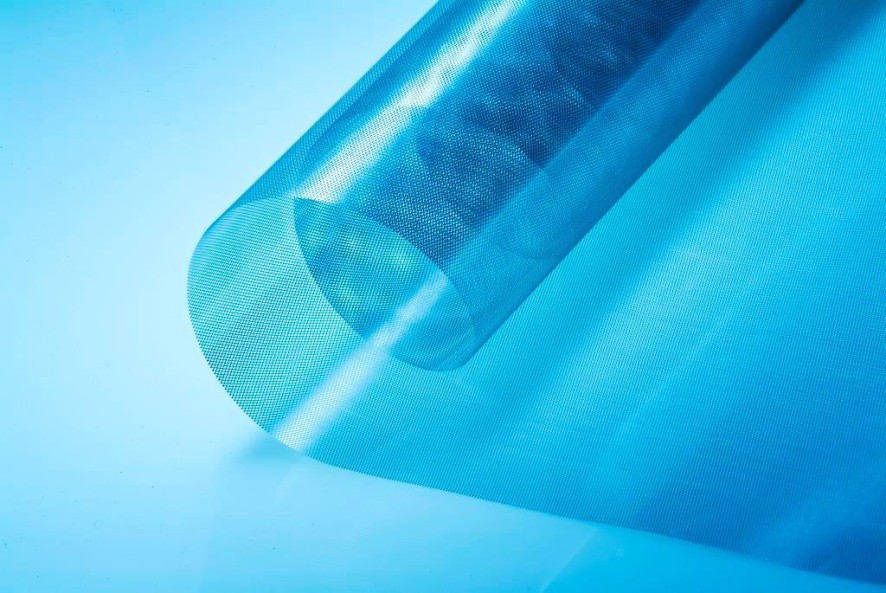
Basement well covers, stents, screens – expanded metal mesh has a variety of uses. Whereas expanded aluminum or copper mesh is often made thinner than a tenth of a millimeter, up to now the limit for steel has been 0.4 millimeters. But now ThyssenKrupp Rasselstein GmbH together with Bender GmbH has developed an expanded metal mesh consisting of only 0.13 millimeter thick steel – or to be more precise tinplate. The advantage: Steel is inexpensive and much stronger than aluminum.
Saving resources is a growing trend, not only in the auto industry. Other industries too are looking at ways to use as little material as possible in their products. One example is expanded metal mesh, made by slitting and stretching a sheet of metal to produce grid structures of the type found in filters, stents and basement window well covers. “Working together with Bender GmbH we have for the first time produced expanded metal mesh from 0.13 millimeter ultra-thin steel,” says Tobias Kirst, a development engineer with ThyssenKrupp Rasselstein. “It’s a pioneering achievement.” Whereas expanded copper mesh is often only 0.03 millimeters thick, the previous limit with steel was 0.4 millimeters. It means the researchers have reduced the thickness of the sheet by roughly 70 percent. But despite this huge material saving the expanded metal remains strong and robust.
“The product stemmed from the idea of developing a material for a disposable steel barbecue grate,” explains Kirst. Cleaning burned-on grease from the grill is not everyone’s idea of fun. Many barbecue fans place aluminum foil under the meat, but it can fly off when there’s nothing on it and you don’t get the typical barbecue flavor. Also, hot oil can collect on the foil and catch fire. But place a thin expanded metal mesh on the grill instead of the foil and the grill will stay clean while the meat cooks, acquiring its typical grill pattern and slightly smoky flavor. And excess oil cannot collect on the steel mesh.
Customers save material and costs
The potential uses of the thin expanded metal are many. The material offers numerous advantages: It is thin and light yet strong and robust. For example it could be used in the production of filters. Filter manufacturers would need less material and save costs. The filters themselves mainly consist of a soft foam material backed usually by an expanded aluminum mesh. In the future manufacturers could use a steel mesh instead. Steel is harder and stronger than aluminum, so thinner meshes would suffice to achieve the required strength. Also, steel is much less expensive than aluminum.
But filters aren’t the only potential use for the thin expanded metal. It can also be used to shield electromagnetic radiation, thanks to a property called electromagnetic compatibility. As an example, cars these days feature more and more electronic devices. To save weight, these often have housings made of composite materials rather than metal. However these composites do not shield the electromagnetic radiation emitted by the devices. This job could be performed with little extra weight by a thin expanded metal mesh.
The thin expanded metal also has potential uses in the building trade – for example in tiling. Here, installers insert either metal laths or plastic mesh to prevent tiles from falling off and taking plaster with them. “Our thin expanded metal combines the advantages of the metal laths with those of the plastic mesh: The expanded metal forms a mesh like plastic but with the strength of steel,” explains Kirst.
Designers could also use the new expanded metal. Color coating the steel foil prior to expanding produces interesting effects. This colored mesh can be used to make lampshades and similar decorative articles.
ThyssenKrupp Rasselstein GmbH is Germany’s only tinplate manufacturer. It is a subsidiary of ThyssenKrupp Steel Europe AG and one of Europe’s three biggest producers of packaging steel. The company produces roughly 1.5 million tons of packaging steel a year, serving around 400 customers in 80 countries. At the world’s biggest production site for packaging steel in Andernach ThyssenKrupp Rasselstein manufactures tin-coated, chromium-coated and organic coated material as well as zinc-coated and uncoated blackplate.
Bender GmbH in Siegen is one of the world’s leading suppliers of expanded metals, established in almost all areas of industry. Unique products have been developed for sectors such as energy, medical, electroplating, chemicals, filters, automotive, aerospace, protective meshes, decoration and household goods. The applications covered include filtering, sealing, protecting, screening, decorating, ventilating and conducting.