Complexity in the car body is reduced
The idea of the cooperation partners is as simple as it is effective: instead of laboriously joining many individual components, a single plate is used to create a tailor-made structural carrier for the outer side wall – the so-called door ring, which, including the A, B, and C pillars, forms the frame for the doors that are later installed in a vehicle. “In simulations with our selectrify® reference car body in the compact class, we were able to demonstrate that up to eight individual components can be integrated into the vehicle structure in this way,” explains Dr. Thomas Böttcher, Head of Application Concepts at thyssenkrupp Steel. This brings enormous advantages: lower costs due to less complexity and less joining work, as well as a weight saving potential of 5.8 kilograms in the case of the reference structure.
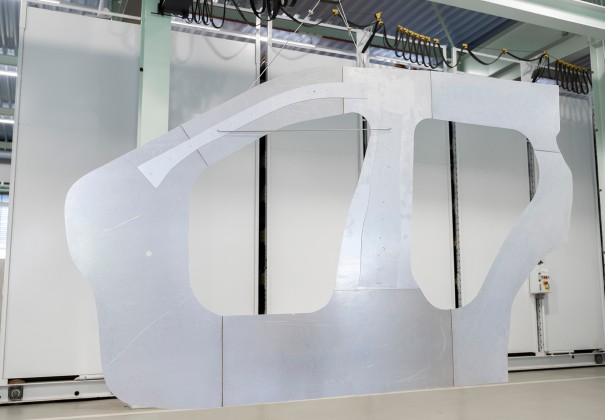
At the heart of the concept is a tailored blank plate into which hot-forming grades of different strengths are integrated in a targeted manner. This means that MBW® 1200 and the AS Pro-coated materials 1500 and 1900 from thyssenkrupp Steel are used precisely where they deliver the greatest benefits: MBW® 1200, for example, is used in both the sill and the foot of the B-pillar, where high ductility is required. MBW® 1900 + AS Pro, on the other hand, is used in the upper safety-relevant zones of the B-pillar with maximum deformation resistance.
Door ring is custom work
But the concept is not only convincing in theory. Its implementation requires enormous technological finesse. The large variations in material thickness are particularly challenging – for example, from 1.8 millimeters to 1.0 millimeter in the area of the A-pillar and sill. These affect the cooling behavior during forming and also place high demands on the laser welding of the blank. Only through the close integration of design, forming simulation, and joining technology was it possible to ensure the manufacturability of the door ring during the course of the project. The GONAtech® welding process developed by Baosteel Tailored Blanks completely eliminates the need for decoating the blanks prior to welding and contributes significantly to economical lightweight construction.
“The combination of our material grades with customized blank designs harmonizes performance and efficiency,” says Thomas Böttcher. “Our project demonstrates how material, manufacturing, and process expertise can be combined synergistically.” This applies not only to the use of steels for hot forming. Highly efficient tailored blank solutions can also be realized with materials for cold forming, such as jetQ® multiphase steels with high strength grades, depending on the manufacturer's preferences. For sustainable automotive engineering, thyssenkrupp Steel also offers its customers all proven steel grades with reduced CO2 intensity under the bluemint® Steel brand.
Cost-efficient lightweight construction
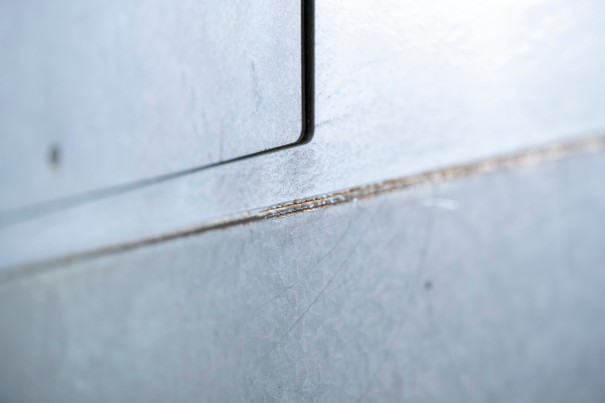
A glance at the automotive industry shows just how important it is for materials partners and experts to address this issue: various well-known vehicle manufacturers are already relying on integrated components and installing large structural components in the bodywork instead of separate components. The advantages are obvious: fewer parts mean fewer interfaces, fewer tools, fewer process materials, shorter cycle times – and ultimately lower manufacturing costs and a reduced carbon footprint. These advantages are demonstrated within the scope of the cooperation, assuming various boundary conditions. The resulting evaluation methods will also be available to customers for inquiries about InPart Solutions in the future.
At the same time, customized, localized material inserts can be used to optimize mechanical properties in a targeted manner – especially in lightweight construction and crash safety. In this context, the door ring not only offers an economically attractive solution, but also supports innovative body concepts, such as modular vehicle platforms.
Strong materials partner for the automotive industry
In addition to the production-related advantages, the fully integrated Door Ring scores points for its lower material usage compared to the basic concept, thereby reducing the CO2 footprint of the vehicle right from the production phase. The exact figures will be calculated in detail in the course of the Door Ring cooperation project. Dr. Thomas Böttcher: “With our InPart Solutions such as the Door Ring, we are underlining our role as an important materials partner and consultant to the automotive industry: through materials with maximum performance, tailor-made solutions for modern manufacturing processes, and an unconditional commitment to supporting the transformation of the industry with innovative concepts.”