Komplexität in der Karosserie wird reduziert
Die Idee der Kooperationspartner ist ebenso simpel wie wirkungsvoll: Statt viele Einzelbauteile aufwendig zu fügen, entsteht aus einer einzigen Platine ein maßgeschneiderter Strukturträger für die äußere Seitenwand – der sogenannte Door Ring, der inklusive A-, B- und C-Säule den Rahmen für die später eingesetzten Türen eines Fahrzeugs bildet. „In Simulationen mit unserer selectrify® Referenzkarosserie der Kompakt-Klasse konnten wir nachweisen, dass so bis zu acht Einzelkomponenten in der Fahrzeugstruktur integriert werden können“, erklärt Dr. Thomas Böttcher, Leiter Anwendungskonzepte bei thyssenkrupp Steel. Das bringt gewaltige Vorteile mit sich: Geringere Kosten durch weniger Komplexität und geringeren Fügeaufwand sowie ein Gewichtseinsparpotenzial von 5,8 Kilogramm im Falle der Referenzstruktur.
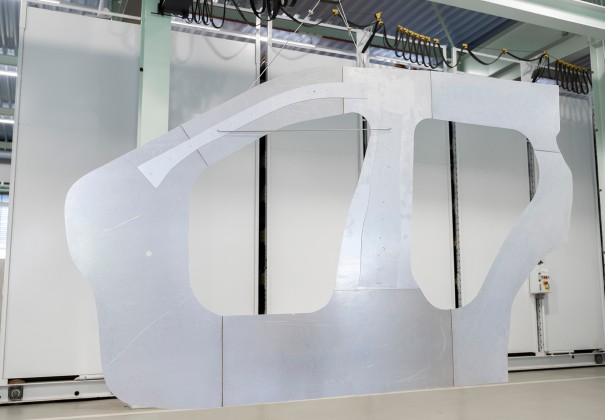
Herzstück des Konzepts ist eine Tailored-Blank-Platine, in die gezielt Warmumformgüten unterschiedlicher Festigkeiten integriert werden. So kommen die Werkstoffe MBW® 1200 und die mit AS Pro beschichteten Güten 1500 und 1900 von thyssenkrupp Steel genau dort zum Einsatz, wo sie den größten Nutzen bringen: MBW® 1200 wird zum Beispiel sowohl im Schweller als auch im Fuß der B-Säule eingesetzt, da hier ein hoher Bedarf an Duktilität besteht. MBW® 1900 +AS Pro hingegen wird in der oberen sicherheitsrelevanten Zonen der B-Säule mit maximalem Deformationswiderstand verbaut.
Door-Ring ist Maßarbeit
Doch das Konzept überzeugt nicht nur in der Theorie. Die Umsetzung verlangt enorme technologische Finesse. Besonders anspruchsvoll sind die hohen Materialdickensprünge – etwa von 1,8 Millimetern auf 1,0 Millimeter zum Beispiel im Bereich von A-Säule und Schweller. Sie beeinflussen das Abkühlverhalten beim Umformen und stellen gleichzeitig hohe Anforderungen an das Laserschweißen der Platine. Nur durch die enge Verzahnung von Konstruktion, Umformsimulation und Fügetechnik konnte die Herstellbarkeit des Door Rings im Projektverlauf abgesichert werden. Das bei Baosteel Tailored Blanks entwickelte Schweißverfahren GONAtech® verzichtet hierbei vollständig auf das Entschichten der Platinen vor dem Schweißprozess und trägt wesentlich zum wirtschaftlichen Leichtbau bei.
„Die Kombination unserer Materialgüten mit maßgeschneiderten Platinendesigns bringt Performance und Effizienz in Einklang“, so Thomas Böttcher. „Wir zeigen mit unserem Projekt, wie sich Werkstoff-, Fertigungs- und Prozesskompetenz synergetisch verbinden lassen.“ Dies gilt nicht nur für den Einsatz von Stählen für die Warmumformung. Auch mit Werkstoffen für die Kaltumformung wie Mehrphasen-Stähle mit hohen Festigkeitsklassen der Marke jetQ® lassen sich hocheffiziente Tailored-Blanks-Lösungen realisieren – je nachdem, was der jeweilige Hersteller bevorzugt. Für den nachhaltigen Automobilbau bietet thyssenkrupp Steel mit der Marke bluemint® Steel seinen Kunden zudem schon heute alle bewährten Stahlgüten in reduzierter CO2-Intensität an.
Kosteneffizienter Leichtbau
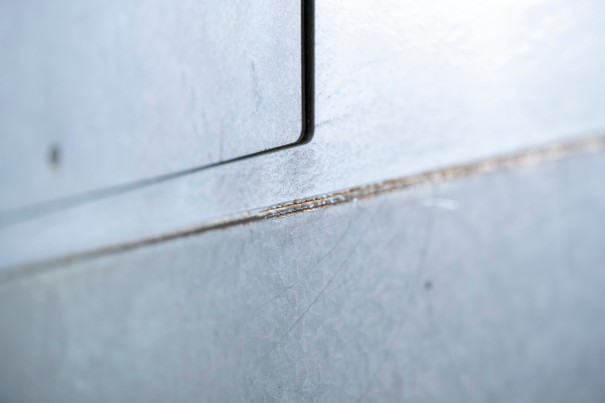
Wie wichtig es für Werkstoffpartner und -experten ist, sich mit dem Thema zu beschäftigen, zeigt ein Blick auf die Autobauer: Schon heute setzen verschiedene namhafte Fahrzeughersteller auf integrierte Bauteile und verbauen statt separaten Komponenten großflächige Strukturbauteile in der Karosserie. Die Vorteile liegen auf der Hand: weniger Teile bedeuten weniger Schnittstellen, weniger Werkzeuge, weniger Prozesswerkstoffe, kürzere Taktzeiten – und letztlich geringere Fertigungskosten sowie einen reduzierten CO2-Footprint. Diese Vorteile werden im Rahmen der Kooperation unter Annahme verschiedener Randbedingungen nachgewiesen. Die entstandenen Bewertungsmethoden stehen künftig auch für Kundenanfragen zu InPart Solutions zur Verfügung.
Zugleich lassen sich durch maßgeschneiderte, lokalisierte Materialeinsätze gezielt mechanische Eigenschaften optimieren – insbesondere im Leichtbau und bei der Crashsicherheit. In diesem Zusammenhang bietet der Door Ring nicht nur eine wirtschaftlich attraktive Lösung, sondern unterstützen auch neuartige Karosseriekonzepte – etwa Fahrzeugplattformen in Modulbauweise.
Starker Werkstoffpartner für die Automobilindustrie
Neben den produktionstechnischen Vorteilen punktet der vollintegrierte Door Ring durch seinen geringeren Werkstoffeinsatz im Vergleich zum Basiskonzept mit Materialeffizienz und reduziert damit den CO2-Fußabdruck des Automobils schon in der Produktionsphase. Wie genau diese aussehen, soll im weiteren Verlauf des Door-Ring-Kooperationsprojekts noch detailliert bilanziert werden. Dr. Thomas Böttcher: „Mit unseren InPart Solutions wie dem Door Ring unterstreichen wir unsere Rolle als wichtiger Werkstoffpartner und Berater der Automobilbranche: Durch Werkstoffe mit maximaler Performance, maßgeschneiderten Lösungen für moderne Fertigungsprozesse sowie den unbedingten Willen, die Transformation der Industrie mit innovativen Konzepten zu begleiten.“