thyssenkrupp Steel has been aware for some time that customers have encountered challenges when combining third-generation high-strength steels. “Resistance spot welding of these new hot-dip galvanized AHSS grades remains one of the most critical process steps in manufacturing,” confirms Patrick Kuhn, Product Manager for Multiphase Steels at thyssenkrupp Steel. The challenges manifest themselves in the potential formation of liquid metal embrittlement, which can lead to cracking in the weld spot. This causes reservations about the use of third-generation AHSS steels on the part of processors and automotive manufacturers. His colleague Melanie Dinter from the steel manufacturer's sales engineering department adds: “We took our partners' comments very seriously and investigated them thoroughly. That is why we have been determining joining parameters for many years as part of our development work in order to provide our customers with application-specific support.”
The key question here is: Can components made from jetQ® grades be reliably welded to other materials using resistance spot welding to form practical components without cracking? To answer this question under practical conditions, thyssenkrupp Steel and its long-standing partner Benteler Automotive Components – a leading international supplier to the automotive industry – initiated a joint test project at the end of 2024.
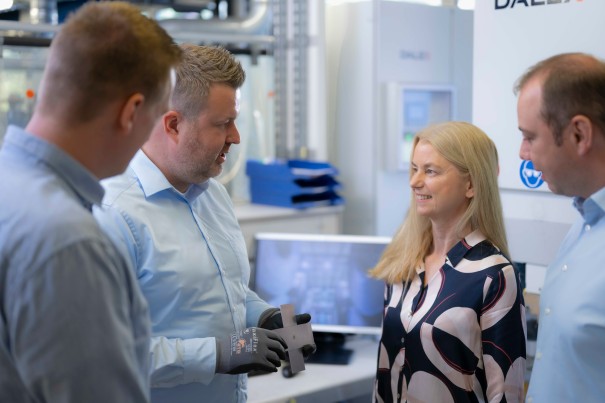
The investigations focused on eight different steel combinations of the jetQ® 980 and jetQ® 1180 brands, each combined with common steels for structural applications from series production. These included particularly demanding variants such as the combination of aluminum-silicon-coated hot-forming steels with hot-dip galvanized cold-forming grades – typical mixed joints found in B-pillars, for example. The actual physical tests were carried out at the Dortmund (thyssenkrupp Steel) and Paderborn (Benteler) sites. While thyssenkrupp Steel carried out the welding processes, Benteler performed the subsequent evaluation using microscopic analyses and tensile tests. The result: Not a single LME-induced crack was detected in over 500 weld points analyzed. This was an extremely positive result that exceeded even the expectations of the Benteler experts.
“LME crack tendency is always an important and sometimes challenging issue when processing hot-dip galvanized AHSS steels,” says Tobias Böddeker, Director R&D Materials Technology at Benteler Automotive Components. “The fact that we were able to demonstrate exclusively crack-free joints in our joint project with thyssenkrupp Steel is an important step toward expanding the series production of these new steels with a tensile strength of 1000 MPa and more.”
The basis for the convincing results is provided by the consistent development work carried out by thyssenkrupp Steel over the past years. “In the run-up to the joint project, robust welding parameters for resistance spot welding for a wide variety of material combinations were determined as part of materials engineering development using the standardized SEP1220-2 process,” explains Sebastian Schulte, the expert responsible for press welding technology at thyssenkrupp Steel. This systematic database made it possible to carry out the tests with practical and reproducible parameters and thus achieve results that can serve as a basis for application in series production.
jetQ® for lightweight construction of the future
The close cooperation between the teams at both companies shows that the project was not only a technical success but also a partnership success. While thyssenkrupp Steel contributed its extensive expertise in materials and process development, the project benefited significantly from Benteler's process expertise and direct access to OEM requirements and real-world applications.
Benteler sees jetQ® as an important addition to its own material portfolio, especially for safety-relevant structural components where previous grades have reached their limits. “Third-generation AHSS steels, which include the new jetQ® grades, offer us and our customers additional freedom in design and engineering, precisely where it is needed,” says Serge Reitz, Global Coordinator in Material Application for Cold-Formed Structural Components at Benteler Automotive Components. OEMs are also showing interest in the third generation of AHSS – provided that joining processes can be implemented reliably and without costly adjustments. “Our joint project has now impressively demonstrated that this is indeed the case,” says the materials expert.
Conclusion: jetQ® 980 and jetQ® 1180 are not only new materials, but also key components for next-generation lightweight construction. What's more, they are suitable for practical use. With the right welding parameters, even demanding material joints can be produced without cracks. This is a key finding that demonstrates how important the interaction of material innovation, process expertise, and partnership-based development is – now more than ever.