Challenge in plant engineering: Coils remember their shape
“To enable us to transport our steel strips to our customers, they are wound into coils using a reel,” explains Bosch. However, the thicker and harder the material, the more force is required to wind the strip. "During this process, the steel becomes deformed, and the coiled steel strip remembers this deformation.
To compensate for this deformation, almost every steel processing plant has at least one straightening machine in the process inlet area. This machine uses several straightening rollers to flatten the delivered steel strip so that it can be further processed optimally and all products manufactured from it are as flat as possible. In practice, however, this process does not always run smoothly. “We then receive a report via our technical customer service department and take another close look at things at the customer's site,” explains Bosch.
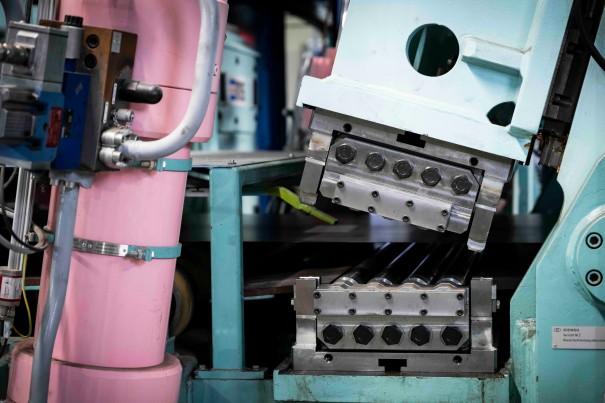
Two aspects can be decisive here: On the one hand, the steel strip itself may be deformed beyond the natural, process-related longitudinal bow. This can be, for example, a longitudinal bow that curves away from the coil, or edge waves. Second, straightening machines are extremely complex systems that differ in terms of their control systems, functions, and capabilities depending on the manufacturer. Depending on the material that needs to be leveled, it can be very difficult to find and set the right parameter adjustments for optimal processing.
But regardless of whether the cause is material-related or technical, Frank Bosch's extensive experience has enabled him to solve almost every challenge, no matter how complicated, and thus avoid complaints. The trained electrical engineer draws on extensive expertise in straightening procedures, which he has acquired over the years thanks to his keen curiosity and creative inventiveness. This has also resulted in a fully automatic straightening machine control system, which is currently being patented by thyssenkrupp Steel.
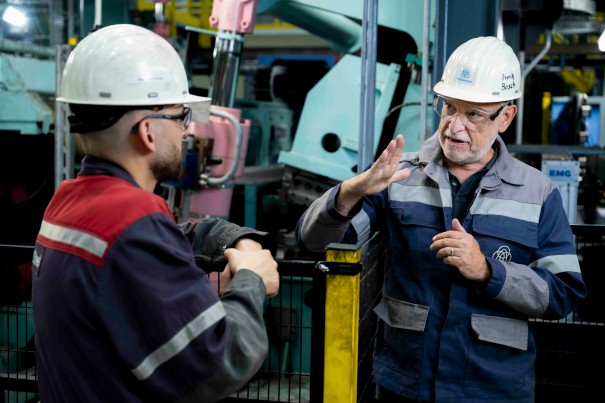
Frank Bosch does not only use the manufacturer- and model-independent expertise he has acquired to quickly solve problems on the straightening machines at customer sites. He also uses it to train the further processing teams in the complex tasks involved in straightening materials. From Germany to Eastern Europe and Asia: When it comes to solving problems at customer sites and sharing his wealth of knowledge with colleagues, Frank Bosch is always on hand. This was recently the case at the Fischerstahl steel service center in Netphen, North Rhine-Westphalia, where the technician helped to eliminate a strip flatness problem on steel sheets for switch cabinets by making new adjustments to the straightening machine and introducing a new testing procedure.
Bosch then held two workshops with Fischerstahl experts to enable the team to solve similar challenges even more effectively in the future.
The response to Bosch's work has been more than positive. An important reason for this is the winning manner of the steel-enthusiast tinkerer, who, despite all the seriousness of the task at hand, always displays a certain relaxed attitude and has never lost his enthusiasm for the subject. “Of course, our primary goal is to get everything up and running as quickly as possible for the customer and to avoid complaints,” says Bosch. However, in order to be perceived as a competent problem solver in direct contact with people, personal and respectful interaction is also very important, emphasizes the Rheinhaus native, adding: “In this way, we not only demonstrate our technical capabilities, but also prove the strong service mentality that distinguishes us as thyssenkrupp Steel.”