Direktreduktionsanlage: Neubau ist Neuland
Die Menschen, die sich bei thyssenkrupp Steel an verschiedenen Stellen darum kümmern, den Wandel zur wasserstoffbasierten Stahlproduktion vorzubereiten, sind sich der Tragweite des Vorhabens bewusst. Einer von ihnen ist Markus Wischermann. Der Diplom-Ingenieur, bisher verantwortlich für die Roheisenerzeugung bei thyssenkrupp Steel, hat im Frühjahr 2023 die Projektleitung für den Bau der ersten Direktreduktionsanlage übernommen. Markus Wischermann mag es, Neuland zu betreten. Dafür zu sorgen, dass der für die Zukunft der Stahlindustrie so wichtige Neubau von Anfang an gut geplant und mit den unterschiedlichsten Gewerken abgestimmt wird, ist genau sein Ding.

„Konkret koordinieren wir aktuell die vorbereitenden Arbeiten auf dem Baufeld. Dazu zählen auch die behördlichen Genehmigungen, die wir brauchen, um demnächst das Fundament der Anlage zu legen“, so Wischermann. „Übergeordnet besteht unsere Aufgabe vor allem darin, alle Projektbeteiligten immer wieder konsequent zusammenzubringen und das Riesenprojekt in eine sehr dezidierte Ablaufstruktur zu bringen. Wir stellen also sicher, dass in der Hochphase jeder Beteiligte genau weiß, was zu tun ist.“
Apropos, Hochphase. Es braucht ein wenig Vorstellungskraft, um sich zu vergegenwärtigen, mit welchem Tempo der Bau der ersten Direktreduktionsanlage auf dem Hafengelände in Duisburg-Walsum ab Januar 2024 voranschreiten wird. Auf der riesigen Brachfläche am Rhein wird binnen drei Jahren ein Industriekomplex entstehen, der es an seiner höchsten Stelle beinahe mit den Türmen des Kölner Doms aufnimmt. Noch allerdings beherrscht hier, zwischen dem markanten Kühlturm des nahegelegenen Kraftwerks und dem weitläufigen Stahlwerksgelände Schwelgern, der graubraune Boden die Szenerie. Lediglich ein paar Bagger lassen sich dabei beobachten, wie sie die letzten Überreste des ehemaligen Brammenlagers ausgraben und abtragen.
Transformation: Planung ist das A und O
Das wird sich 2024 ändern: Bis zu 1.500 Menschen aus unterschiedlichen Unternehmen werden dann drei Jahre lang parallel auf der Baustelle arbeiten. „Das sind die Mitarbeitenden der SMS Group, die für den Bau der Anlage und die Ausgestaltung der technologischen Details verantwortlich sind. Außerdem der Generalunternehmer, der die Fundamente setzt, aber auch alle weiteren Gebäude auf dem Gelände plant und umsetzt. Und dann kommen auch die Kolleginnen und Kollegen aus unseren eigenen Betrieben dazu, die zum Beispiel Wege und Lager planen, um die Anlage mit Energie und Materialien zu versorgen“, so Markus Wischermann. „Diese Menschen zu koordinieren und im Vorhinein dafür zu sorgen, dass jeder einzelne Schritt gut durchgeplant ist und auch in puncto Arbeitssicherheit alles rundläuft, das ist eine gewaltige Aufgabe.“
Auch Markus Wischermann braucht ein gutes Vorstellungsvermögen: Wo genau wird das benötigte Material am Hafen angelandet? Was wird zwischengelagert? Welche Instandhaltungsprozesse müssen bei der Wege- und Gebäudeplanung bedacht werden? Um alle diese Fragen nicht nur frühzeitig, sondern auch kompetent zu beantworten, nimmt der Koordinator an den regelmäßigen Treffen im „Green Transformation Office“ teil. Dort kommen Teams aus unterschiedlichen Abteilungen zusammen, um sich abzustimmen und gegenseitig auf dem neusten Stand zu halten. Begleitend dazu informiert thyssenkrupp Steel die Nachbarschaft in regelmäßigen Bürgerdialogen über den Fortgang des Projekts.
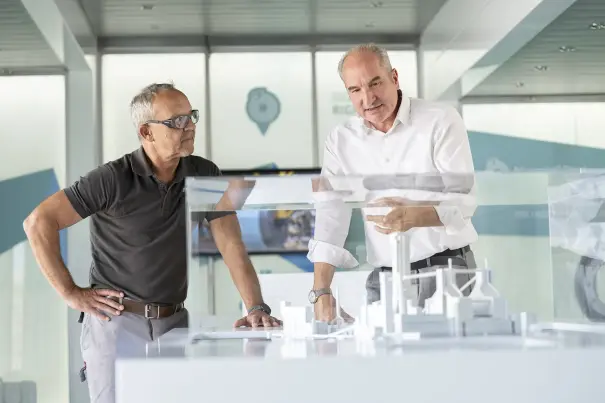
Dr. Matthias Weinberg vertritt im Transformationsprojekt die technologische Perspektive. Der Leiter des Competence Center Metallurgy und seine Mitarbeitenden erarbeiten die Grundlagen für den wasserstoffbasierten Betrieb der DR-Anlage und der angeschlossenen Einschmelzaggregate. Dass die elf Kollegen intern vor allem als „Ocean’s Eleven“ bekannt sind, zeigt Matthias Weinberg, dass die HR-Abteilung bei der Auswahl der Teammitglieder einen sehr guten Job gemacht hat. „Bei uns kommen etliche Expertisen zusammen, darunter Chemie, Metallurgie, Maschinenbau, Verfahrens- und Elektrotechnik“, erklärt der Werkstoffspezialist. „Dieser weite Blickwinkel ist sehr wichtig, um neuartige und komplexe Verfahrensfragen zu beantworten.“
Im Kern geht es um die Frage, wie sich der Wasserstoff im Reaktor verhält. Dazu prüfen die Experten in umfangreichen Versuchsreihen, welchen Einfluss unterschiedliche Einsatzstoffe auf die Reaktionsgeschwindigkeit und letztlich auf die Qualität der Endprodukte haben. „Man darf nicht vergessen, dass eine Direktreduktionsanlage in dieser Größe noch nie zuvor mit Wasserstoff betrieben worden ist“, betont der Metallurge. thyssenkrupp Steel nennt es „first of it's kind“, da diese Kombination von DR-Anlage mit Einschmelzern weltweit erstmals umgesetzt wird.
Die DR-Anlagentechnologie selbst wird dagegen seit Jahrzehnten in aller Welt eingesetzt. Auch thyssenkrupp Steel besaß in den 1980er Jahren eine Direktreduktionsanlage, die jährlich 100.000 Tonnen Roheisen produzierte. Betrieben wurde sie mit Erdgas. „Wasserstoff galt schon immer als teurer Energieträger und wurde daher nur in der akademischen Forschung eingesetzt“, so Weinberg. „Folglich beschäftigen wir uns schon seit geraumer Zeit mit allen erdenklichen entwicklungstypischen Risiken, die der Betrieb mit Wasserstoff mit sich bringen könnte. Manche dieser Fragestellungen untersuchen wir in unseren werkseigenen Laboren. Für andere brauchen wir einen größeren Maßstab, denn nur so erhalten wir übertragbare Ergebnisse. Bis unsere eigene Versuchsanlage steht, arbeiten wir mit Partnern zusammen, auf deren Anlagen wir im Realbetrieb spezifische Versuchsreihen fahren können.“
Spezifisches Wissen zu Wasserstoff erforderlich
Ein weiterer Arbeitsschwerpunkt des Teams besteht darin, Erkenntnisse aus der Verwendung von Einschmelzaggregaten auf die Roheisenerzeugung zu übertragen. Auch hier gilt: Nicht das Schmelzverfahren an sich ist neu, sondern der Kontext, in dem es verwendet wird. Matthias Weinberg: „Im Gegensatz zu klassischen Elektrolichtbogenöfen, die chargenweise betrieben werden, haben wir hier ein kontinuierliches Einschmelzen von Direct-Reduced Iron mithilfe von Strom. Auch ein Abstechen von erschmolzenem Metall und der Schlacke ist ähnlich wie beim Hochofen nötig.“
In der Nichteisenmetallurgie wird das Verfahren unter anderem genutzt, um Legierungen aus unterschiedlichen Metallen zu erzeugen, darunter Ferronickel oder Ferromangan-Verbindungen, die im Vergleich zu den Eisenerzen aus der Direktreduktionsanlage unter anderem einen deutlich höheren Anteil an Schlacken produzieren. Mit anderen Worten: Beim Einschmelzen von Roheisen müssen wesentliche Prozessparameter neu justiert werden. Matthias Weinberg ist dennoch überzeugt: Eine bessere Lösung als die von thyssenkrupp Steel gewählte Kombination aus Direktreduktion und Einschmelzaggregaten gibt es nicht. Denn im Vergleich zu anderen Verfahren bereiten Schlacken den Schmelzanlagen keine Probleme. Das wiederum bedeutet, dass die kompakten Aggregate mit unterschiedlichen Eisenerzqualitäten zurechtkommen. „Wir sind deshalb nicht darauf angewiesen, nur besonders hochwertige Eisenpellets einzukaufen.
Und das ist gut, denn in diesem Markt zeichnet sich schon heute ein Engpass ab, der den Preisdruck erhöht.“ Lieber als in spezielle Erze investiert der Stahlproduzent in den Aufbau spezieller Expertisen. „Wir brauchen Menschen, die die Grundlagen und Rahmenbedingungen für den effizienten Einsatz des neuen Verfahrens erarbeiten“, sagt der Leiter des Competence Center Metallurgy. „Kluge Köpfe, die explorativ vorgehen und geübt darin sind, sich neuen Herausforderungen systematisch anzunähern. Vor allem aber brauchen wir Ingenieure und Techniker, die ihr Wissen gut an andere weitergeben können. Denn es ist anspruchsvoll, mit Wasserstoff zu arbeiten, jeder im Unternehmen benötigt dazu spezifisches Wissen – vom Vorstand bis hin zu den Kollegen im Leitstand, die für den täglichen Betrieb der Anlage zuständig sind.“
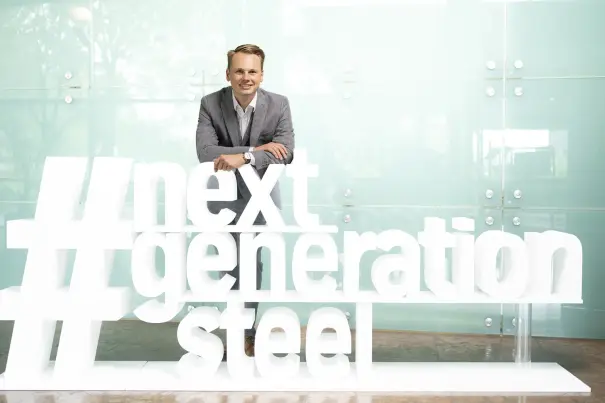
Wasserstoff. Im Berufsalltag von Henning Weege spielt der Energieträger der Zukunft bereits heute eine zentrale Rolle. Als Head of Hydrogen & Green Energy besteht seine Aufgabe unter anderem darin, den Wasserstoffbedarf seines Arbeitgebers durch den Einkauf möglichst vieler grüner Moleküle zu decken. In Kürze startet bei thyssenkrupp Steel die offizielle Ausschreibungsphase. „Unser Ziel ist es, im nächsten Jahr verbindliche Verträge abzuschließen. Dann bleiben den Lieferanten noch gut drei Jahre Zeit, um die entsprechenden Produktions- und Transportkapazitäten aufzubauen“, erzählt Henning Weege.
Bei der Umstellung kann thyssenkrupp Steel seinen Standortvorteil im Herzen des Industriedreiecks Rhein-Ruhr ausspielen. Hier, nah an den ehemaligen Kohleförderstätten, arbeiten Energieerzeuger und -verbraucher seit Jahrzehnten Hand in Hand. Folglich gibt es in der Region bereits ein weit verzweigtes Netz an Erdgasleitungen, durch die perspektivisch auch der Wasserstoff zu den Abnehmern kommen wird. „Unter dem Namen GET H2 entsteht hier gerade das erste öffentlich zugängliche Wasserstoffnetz in Deutschland“, so Henning Weege. „Es führt von Lingen in Niedersachsen bis nach Gelsenkirchen. Am Ausgangspunkt soll künftig mithilfe von Wind- und Sonnenkraft grüner Wasserstoff produziert und dann zu den industriellen Abnehmern ins Ruhrgebiet transportiert werden.“
GET H2 (siehe Infokasten) ist nur ein Baustein im deutschlandweiten Wasserstoff-Kernnetz, das zurzeit von den Fernleitungsnetzbetreibern modelliert und im Herbst 2023 von der Bundesregierung verabschiedet wird. Das Netz soll bis 2032 alle großen Wasserstoff-Einspeiser mit den industriellen Verbrauchern verbinden und wird voraussichtlich zu 60 Prozent aus umgestellten Erdgasleitungen bestehen. Lücken werden durch Neubauprojekte geschlossen. Dazu zählt auch die Wasserstoffleitung DoHa: eine 40 Kilometer lange Pipeline zwischen Dorsten und Duisburg-Hamborn, die thyssenkrupp Steel in das neue regionale Wasserstoffnetz integriert. Weniger als vier Jahre sind für die Umsetzung veranschlagt, 2027 soll DoHa in Betrieb gehen. Der Zeitplan passt zur Inbetriebnahme der DR-Anlage, die nach einer sukzessiven Umstellungsphase ab 2029 zu 100 Prozent mit grünem Wasserstoff laufen soll.
Wasserstoffwirtschaft: „Müssen jetzt starten“
In der Zwischenzeit müssen auch die Spielregeln für die Wasserstoffversorgung festgelegt werden. Klärungsbedarf gibt es unter anderem zur Höhe von Netzentgelten und zu der Frage, wer die Risiken im Bereich des Netzaufbaus trägt. Henning Weege: „So, wie wir keine Garantie dafür haben, dass uns der Markt unseren grünen Stahl auch wirklich abnimmt, müssen auch die Netzbetreiber jetzt in Vorleistung gehen. Dazu braucht es regulierende Spielregeln, die den Markt für alle Teilnehmer gleichermaßen fair und transparent gestalten.“ Für sich und die Kollegen hofft der Stratege vor allem auf eine gleichmäßige und stabile Versorgung mit Wasserstoff. Dies wiederum bedeutet, dass es innerhalb der Infrastruktur genügend Speicher geben muss, um die Schwankungen bei der Produktion von grüner Energie auszugleichen. „Andernfalls müssten wir für den Übergang auf blauen Wasserstoff ausweichen, um die Volatilität auszugleichen.“
Auch wenn es in der Planung immer wieder Unwägbarkeiten gibt, freut sich Henning Weege über die vielen kleinen und großen Schritte, die er gemeinsam mit den Kollegen im Green Transformation Office bereits zurückgelegt hat. Ob alles so rund laufen wird wie geplant? Sicher nicht. „Aber ich bin davon überzeugt, dass wir jetzt starten müssen, um alle Probleme, die kommen werden, frühzeitig zu sehen und Lösungen zu finden“, sagt der Optimist. „Darauf sind wir bestens vorbereitet.“