Premiumqualität und herausragender Service
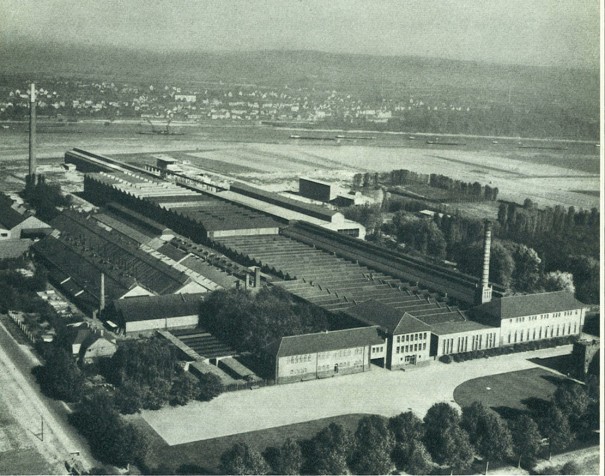
Die Erfolgsgeschichte begann auf der gegenüberliegenden Seite des Rheins. Als Namensgeber diente der Rasselstein, ein Steinbruch in Neuwied. Im Jahr 1760 pachtete der Unternehmer Heinrich Wilhelm Remy „den Rasselstein“ und die Blechfabrik am Aubach mit Zinnhaus. Neun Jahre später wurde dort das erste deutsche Blechwalzwerk in Betrieb genommen. Nach zahlreichen zukunftsweisenden Projekten in der Eisen- und Stahlverarbeitung, wie beispielsweise dem Walzen der Schienen für die erste deutsche Eisenbahnstrecke von Nürnberg nach Fürth, schloss sich das Unternehmen 1916 dem Kölner Eisenwaren- und Schrotthändler Otto Wolff an, der enge Geschäftsbeziehungen zu den Kölner Stahlwerken van der Zypen geschlossen hatte. Gemeinsam beschloss man die Errichtung eines Joint Ventures auf der linken Rheinseite. Im Jahr 1920 wurde das Bandstahlwerk „Remy, van der Zypen & Co.“ in Andernach realisiert und ein Jahr später die Produktion aufgenommen. Es war ausschließlich auf die Verarbeitung von Stahlbändern – heute Warmband genannt – ausgelegt. Damit wurde die Grundlage für die moderne Weißblechproduktion in Andernach gelegt.
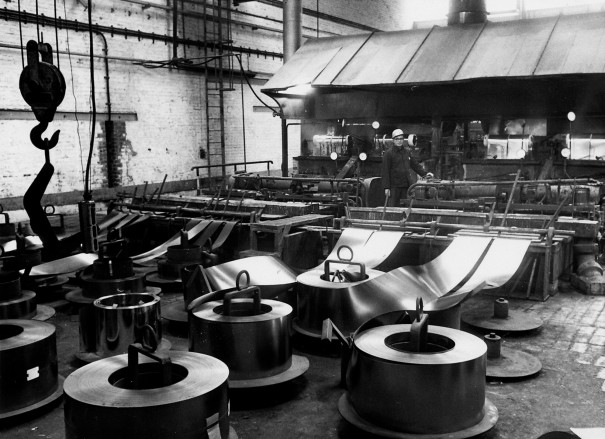
Nach Ende der Inflationszeit gelang es, den Betrieb innerhalb eines Jahrzehnts zu einem der modernsten Weißblechwerke auszubauen. Ein Meilenstein in der Weißblech-Historie wurde im Jahr 1934 mit der Inbetriebnahme der ersten elektrolytischen Bandverzinnungsanlage der Welt erreicht, die das Unternehmen entwickelt hatte. Damit wurde ein Standard geschaffen, der nach dem Zweiten Weltkrieg weltweit übernommen wurde. Im Jahr 1951 folgte die Neugründung der Stahl- und Walzwerke Rasselstein/Andernach AG und 1955 die Inbetriebnahme des ersten Durchlaufglühofens in Europa für das kontinuierliche Glühen von Stahlbändern mit horizontaler Bandführung. Weitere Prozessinnovationen schlossen sich an, zum Beispiel die erste fünfgerüstige Kaltwalz-Tandemstraße in Deutschland im Jahr 1960. Es wurde aber auch immer klarer, dass die Strategie der Innovationsführerschaft einen starken Partner benötigte, den man 1958 mit der August Thyssen-Hütte AG fand. Im Jahr 2003 beschloss der Mutterkonzern – inzwischen die thyssenkrupp AG - den Ausbau des Andernacher Werks auf eine Jahreskapazität von rund 1,5 Millionen Tonnen Weißblech. Seitdem ist das Werk weltweit der größte Produktionsstandort für Weißblech.
In seiner langen Geschichte war das Unternehmen immer am Puls der Zeit, entwickelte innovative Verpackungsstähle und Herstellungsverfahren oder wendete zukunftsorientierte Produktionsprozesse frühzeitig an. Als einer der Technologieführer für Verpackungsstahl hat sich das Unternehmen nie auf dem erreichten Stand der Technik ausgeruht, sondern beständig an neuen Materialeigenschaften und Herstellungsverfahren geforscht, um seinen Kunden hochqualitativen Premiumverpackungsstahl zu liefern. Auch in der näheren Vergangenheit wurden zahlreiche Innovationsprojekte umgesetzt.
Jubilar mit Innovationen im Gepäck
Eine dieser Produktinnovationen ist rasselstein® Solidflex – ein Material, das zugleich hart, aber auch umformfähig ist. Mit einer Dehnung von mehr als fünf Prozent und Streckgrenzen von 600 MPa bis 750 MPa eignet sich rasselstein® Solidflex besonders für Anwendungen, die neben hohen Materialfestigkeiten auch ein erhebliches Umformpotential erfordern – wie zum Beispiel Easy Open Ends oder Aerosoldosendeckel und -böden. Der Clou: Der Einsatz dieses zukunftsweisenden Verpackungsstahls kann darüber hinaus Dickenabsenkungen ermöglichen und somit die Effizienz einer Verpackung deutlich steigern.
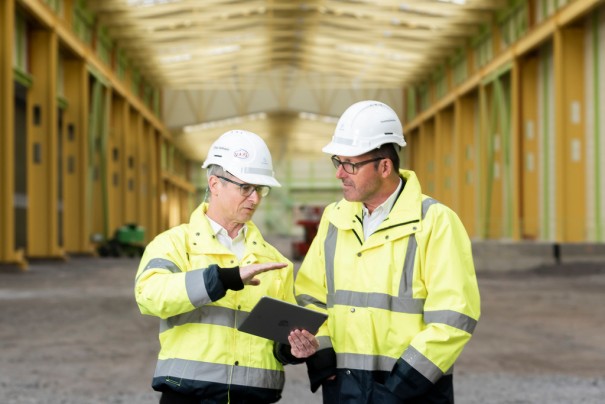
Aber auch Prozessinnovationen stehen im Fokus der Unternehmensstrategie. Aktuell entsteht auf dem Werksgelände eine hochmoderne Veredelungsanlage für spezialverchromten Verpackungsstahl, der vor allem zur Herstellung von Deckeln und Böden für Tiernahrungsdosen, Ventiltellern auf Aerosoldosen, Kronkorken oder Druckfarbendosen eingesetzt wird. Ab 2022 wird Feinstband dort nach einem innovativen Verfahren spezialverchromt. Die neue Beschichtungstechnologie namens Trivalent Chromium Coating Technology (TCCT) basiert auf Chrom(III) anstelle des bisher üblichen Chrom(VI) und erfüllt somit die Vorgaben der EU-REACH-Verordnung. Das Verfahren fußt auf einem Patent von Tata Steel Ijmuiden B.V. und wurde von thyssenkrupp Rasselstein in einem gemeinsamen Technologie-Team mit dem Lizenzgeber weiterentwickelt. Mit der Investition im dreistelligen Millionenbereich setzt das deutsche Unternehmen weiter auf Nachhaltigkeit, Prozess-Effizienz und Qualität. Technologisch wird die neue Veredelungsanlage mit ihrer Fertigstellung die modernste Produktionslinie ihrer Art sein – auch, weil mit dem digitalisierten Workflow zusätzlich effizientere und energiesparende Prozesse realisiert werden.
Rasselstein hat die Zukunft fest im Blick
Der deutsche Weißblechhersteller steht seit jeher aber nicht nur für höchste Produktqualität, sondern auch für beste und vor allem persönliche Kundenberatung sowie für seine Kompetenznetzwerke entlang der Wertschöpfungskette. Da eine Digitalisierung der Prozesse und der Produktion in der Zukunft noch wichtiger werden, hat das Unternehmen eine Reihe von digitalen Services entwickelt, die den Kunden einen Mehrwert bieten und Prozesse vereinfachen, wie rasselstein® Express. Über den Webshop www.packingsteelshop.com können Bestandskunden Zusatzmengen schnell und flexibel online bestellen – immer mit dem Versprechen, dass rasselstein® Express innerhalb von 14 Tagen versandbereit ist.
„Neben bestehenden digitalen Angeboten haben wir bereits weitere innovative Services in der Pipeline“, so Dr. Peter Biele, CEO der thyssenkrupp Rasselstein GmbH. „Wir werden dem Kunden eine Online-Produktkonfiguration und ein neues, flexibles Service-Tool zur Unterstützung unserer Technischen Kundenberatung anbieten. Die persönliche Beratung ist und bleibt aber auch in der Zukunft der wichtigste Bestandteil unseres Service-Angebots.“
Rasselstein setzt auf Nachhaltigkeit und Klimaschutz
Stillstand ist für thyssenkrupp Rasselstein in den letzten 100 Jahren auch ein Fremdwort gewesen, wenn es um die Nachhaltigkeit des Produkts Weißblech ging. Gemeinsam mit der Muttergesellschaft arbeitet das Unternehmen aktuell daran, das Produkt Verpackungsstahl noch nachhaltiger herzustellen – Stichworte sind dabei „Green Steel“ oder „klimaneutraler Stahl“. Hierfür wurden durch thyssenkrupp Steel bereits erste Pflöcke gesetzt: So soll künftig anstelle Kohlenstoff Wasserstoff als Reduktionsmittel im Hochofenprozess eingesetzt werden. Auf diese Weise wird bei der Stahlherstellung dann Wasserdampf statt CO2 freigesetzt. Zugleich wird das Unternehmen bereits entstandene Treibhausgase in wertvolle Chemieprodukte wie Methanol oder Ammoniak umwandeln. Ziel ist es, bis 2045 die Stahlproduktion CO2-neutral zu machen.
„Wir sind stolz, dass wir den innovativen Grundgedanken seit Unternehmensgründung fortführen und nun bereits auf 100 Jahre Rasselstein in Andernach zurückblicken können. Wir haben zahlreiche Investitionen getätigt, um unseren Kunden die bestmögliche Qualität so nachhaltig wie möglich zu liefern. Doch wir haben nicht nur in Anlagen, neue Produkte und digitale Services investiert, sondern auch in unsere Mitarbeiter - wir haben eine Kindertagesstätte auf dem Betriebsgelände eröffnent. Auch in Zukunft möchten wir diesen Weg weitergehen und am weltweit größten Produktionsstandort für Weißblech Innovation durch Investitionen, Qualität, Service, Digitalisierung und das Engagement unserer Mitarbeiter vorantreiben“, sagt Dr. Peter Biele, CEO der thyssenkrupp Rasselstein GmbH.