Premium quality and outstanding service
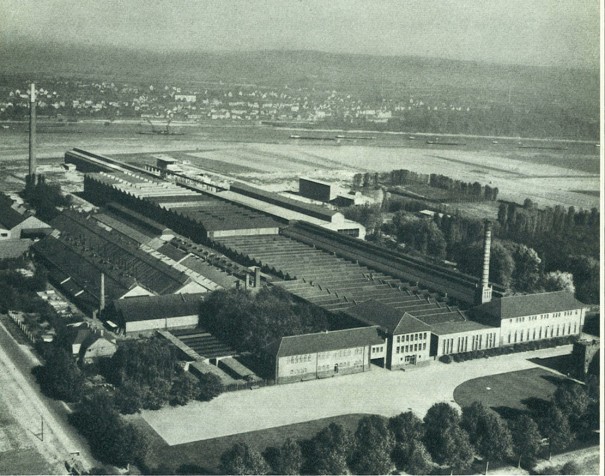
The success story started on the opposite side of the Rhine. Rasselstein was named after a quarry in Neuwied. In 1760, the entrepreneur Heinrich Wilhelm Remy leased the “Rasselstein” and the sheet metal factory with its associated tinworks on the Aubach. The first German plate rolling mill was commissioned nine years later. After carrying out a series of leading-edge iron and steel processing projects, such as rolling the rails for the first German steam railway line running from Nuremberg to Fürth, in 1916 the company joined forces with Otto Wolff, an iron trader and scrap dealer from Cologne, who had close business ties with the Cologne-based steel mill van der Zypen Together they decided to set up a joint venture on the left bank of the Rhine. The strip steel mill Remy, van der Zypen & Co. was built in Andernach in 1920 and started up production one year later. It was designed exclusively to process steel strip, otherwise known as “hot rolled strip” today and laid the foundation for modern tinplate production in Andernach.
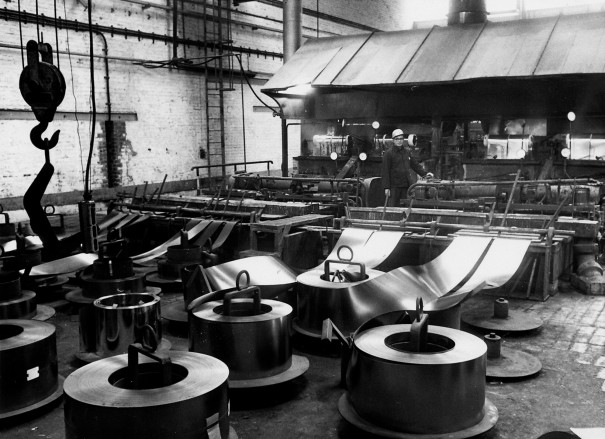
After the end of a period of inflation, the company succeeded in expanding to become one of the most modern tinplate plants in just a decade. In 1934, the company developed and commissioned the world’s first electrolytic strip tinning line, marking a milestone in the history of tin plating and creating a standard that was adopted around the globe after the Second World War. The Rasselstein/Andernach AG steel and rolling mill was re-established in 1951, and Europe’s first continuous horizontal-pass annealing line for wide strip was commissioned in 1955. Additional process innovations, such as Germany’s first five-stand tandem cold-rolling mill in 1960, followed thereafter. It became increasingly clear, however, that the company’s strategy of taking a leading role in innovation required a strong partner, who was found in 1958: August Thyssen-Hütte AG. In 2003, the parent company – now known as thyssenkrupp AG – decided to expand the Andernach plant’s capacity to around 1.5 million tons of tinplate. The plant has been the largest tinplate production site in the world since then.
Throughout the company’s long history, it has always stayed at the forefront of progress, developed innovative packaging steel and manufacturing processes, and applied forward-looking production processes early on. As one of the technology leaders for packaging steel, the company has never taken the state-of-the-art technology it has attained for granted but has continuously researched new material properties and production processes to supply its customers with top-quality premium packaging steel. A variety of innovation projects have also been implemented in the recent past.
rasselstein® Solidflex – a hard yet formable material
rasselstein® Solidflex can be elongated by more than five percent and has yield strengths of 600 MPa to 750 MPa, making it perfect for applications requiring a high material strength as well as good forming properties, such as easy-open ends and aerosol can tops and bottoms. The ingenious twist here is that using this cutting-edge packaging steel also enables the thickness to be reduced, which in turn allows packaging efficiency to be significantly increased.
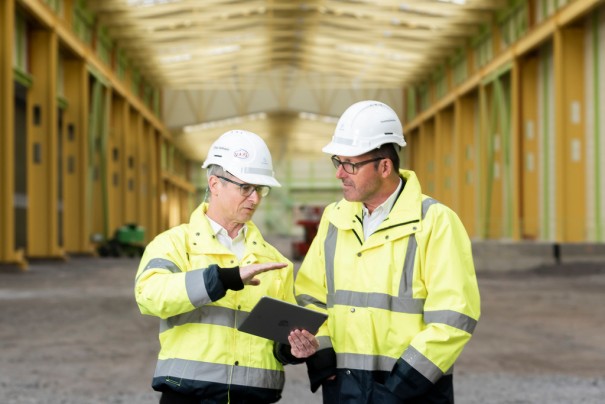
The company strategy also focuses on process innovations. An ultramodern coating facility for special chromium-coated packaging steel is currently being constructed at the plant site. The chromium-coated packaging steel will be used mainly to produce items such as ends for pet food cans, mounting cups on aerosol cans, crown corks and offset ink tins. This is where blackplate will be chromium-coated in line with an innovative procedure from 2022 onwards. The new coating technology – called Trivalent Chromium Coating Technology (TCCT) – uses chromium(III) instead of the so far used chromium(VI) and meets the specifications of the EU’S REACH regulation. The technology is based on a patent from Tata Steel Ijmuiden B.V. and was further developed by thyssenkrupp Rasselstein and the licensor in a joint technology team. The German company is investing hundreds of millions Euros to continue to promote sustainability, process efficiency and quality. From a technological perspective, the new coating facility will be the most modern production line of its kind once it is completed, especially because additional processes that focus on efficiency and energy-saving will be implemented using the digitalized workflow.
Rasselstein has the future firmly in its sights
The German tinplate manufacturer has always stood for the highest product quality but also for the best and, above all, personal customer service and for its networks of excellence along the value chain. With digitalization of processes and production becoming increasingly more important in the future, the company has developed a series of digital services, such as rasselstein® Express, to offer customers added value and to simplify processes. Existing customers can order additional quantities quickly and flexibly online from the webshop www.packingsteelshop.com – and the company promises to ship rasselstein® Express packaging steel always within 14 days.
“Aside from existing digital offers, we’ve already got other innovative services in the pipeline,” said Dr. Peter Biele, CEO of thyssenkrupp Rasselstein GmbH. “We will offer customers an online product configuration and a new, flexible service tool to support our technical customer service. But personal consulting is, and will always be, the most important part of our range of services.”
Rasselstein focuses on sustainability and climate protection
Over the past 100 years, the word “standstill” has never been part of thyssenkrupp Rasselstein’s vocabulary when looking at the sustainability of its tinplate product. The company is presently collaborating with the parent company to produce packaging steel in an even more sustainable manner, emphasizing “green steel” or “climate-neutral steel” in the process. thyssenkrupp Steel has already laid the groundwork for this: In future, hydrogen will replace carbon as the reducing agent in the blast furnace process to release steam instead of CO2 during the production of steel. The company will thus also be able to convert greenhouse gases that have already been created into valuable chemical products such as methanol or ammonia. The objective is to achieve carbon-neutral steel production by 2045.
“We are proud that we have continued the innovative core principles pursued at the time of the company’s foundation and can now look back on 100 years of Rasselstein in Andernach,” continues Dr. Biele. “We have made numerous investments to provide our customers with the highest possible quality in the most sustainable way possible. We have not only invested in machines, new products and digital services, but also in our workforce - we have opened a daycare center on the company site in August. We want to keep to this path in the future and to drive innovation at the world’s largest tinplate production site through investments, quality, service, digitalization and employee dedication.”