We offer verified solutions for the steel industry
In the development of materials and surfaces, processes and applications, the steel business of thyssenkrupp draws among other things on its chemical laboratories as well as pilot plants and application technology simulation tools. The full-service package includes process analysis and operational tests to optimize processes, testing and acceptance of products, providing technical support and assisting with the series production of new products.
Materials & Surfaces
Innovative materials
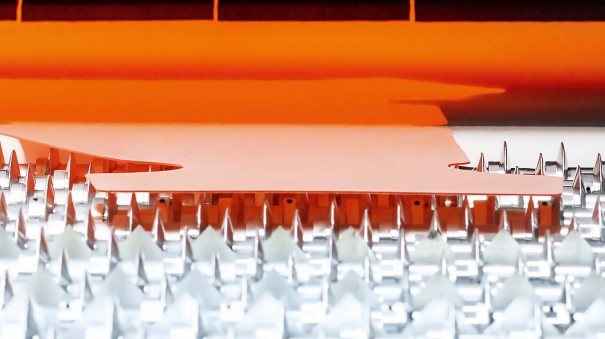
With AS Pro, a new hot forming product, thyssenkrupp Steel is the first steel manufacturer to launch a new, game-changing coating for hot forming ultra-high-strength MBW® steels worldwide – to ensure maximum automobile process and component reliability.
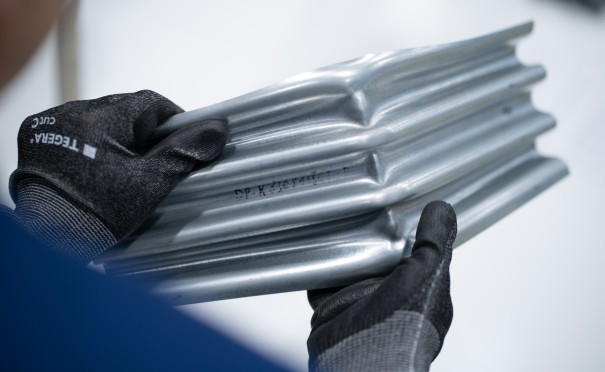
jetQ® stands for a new generation of multiphase steels (AHSS) for vehicle construction. The material combines lightweight construction requirements with maximum crash safety. Compared to other high-strength steels, it has a higher yield strength combined with greater toughness. It is also characterized by a balanced relationship between local and global formability. jetQ® was developed in technical cooperation q1 with the Japanese steel manufacturer JFE and is currently available in strength classes 980 and 1,180.
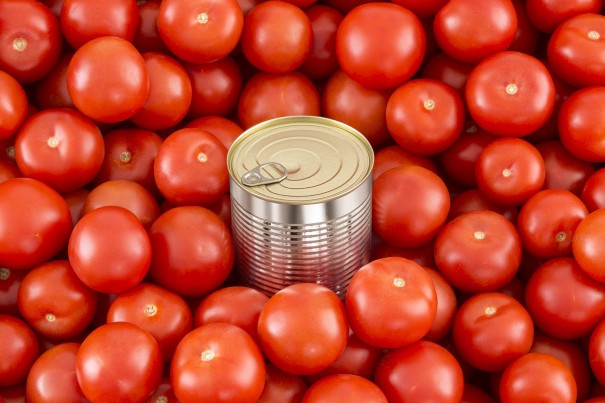
thyssenkrupp Rasselstein now offers its customers rasselstein® CFPA, a 100-percent chromium-free passivation on the surface of tinplate. The innovative product ready for series production offers the same functionality as the previous chromium-based passivations.
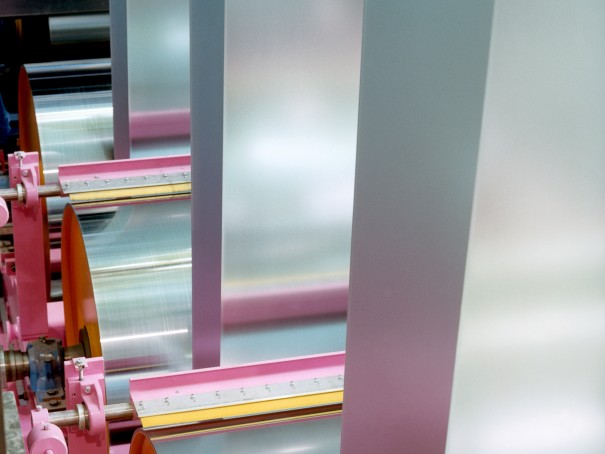
ZM Ecoprotect® is another solutions-oriented material. The novel zinc-magnesium coating is perfectly suited for interior and exterior automobile parts and offers all-round protection for auto bodies. The coating for the external visible components offers particularly high corrosion protection and reduces creep corrosion– in particular on areas of cut edges und scratches, both of which are in danger of rusting to a high degree. Moreover, ZM Ecoprotect® delivers improved formability, reduces adhesive wear in the die and ultimately reduces downtimes for die cleaning.
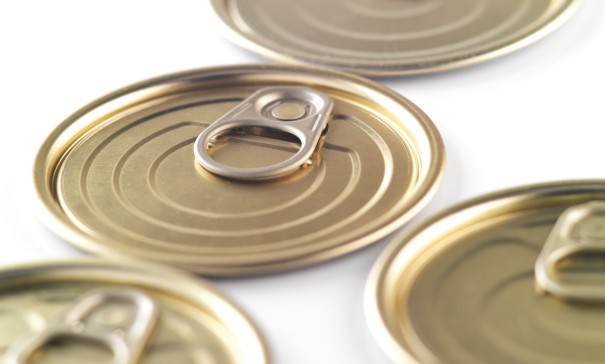
We have developed rasselstein® Solidflex for the packaging industry. This innovation allows to produce tin can packaging that is lighter, more stable, safer, and more sustainable in the future.
Processing methods
Solutions-oriented processing
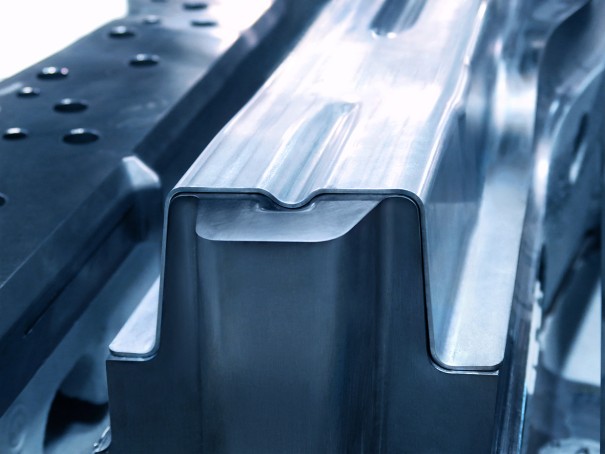
Besides the development of materials, we also develop solutions-oriented production processes for our customers. Our new and innovative production process smartform® allows to produce dimensionally accurate parts, while optimizing costs through a significantly reduced amount of material used and increasing geometric freedom for complex parts.
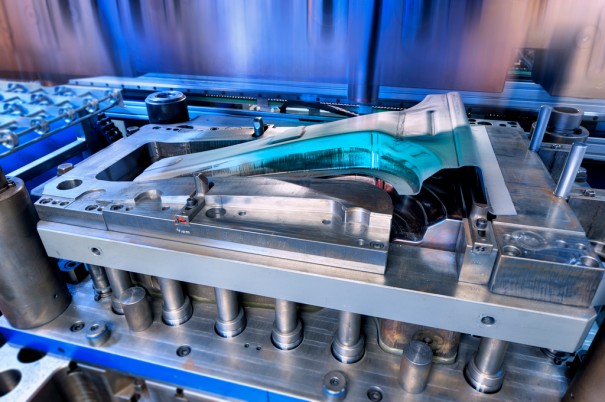
Our patented Tailored Tempering process for hot forming produces hot forming components combining locally different properties in terms of strength and ductility in one monolithic part – in one single process step (tool) and from a hot forming steel blank.
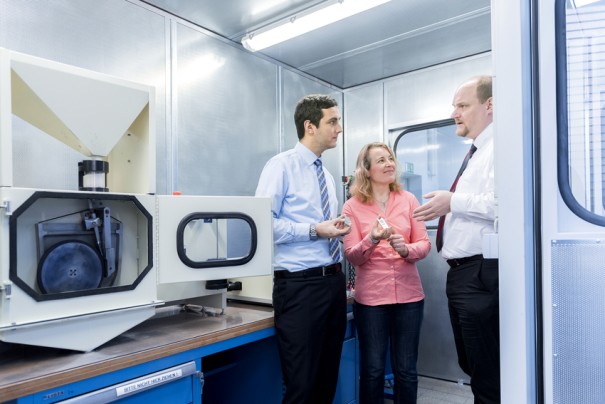
On our model and simulation system, with which it is possible to reproduce the hot forming process exactly, our customers can easily test how sheets will behave in their own hot forming processes – without having to stop their own production lines.
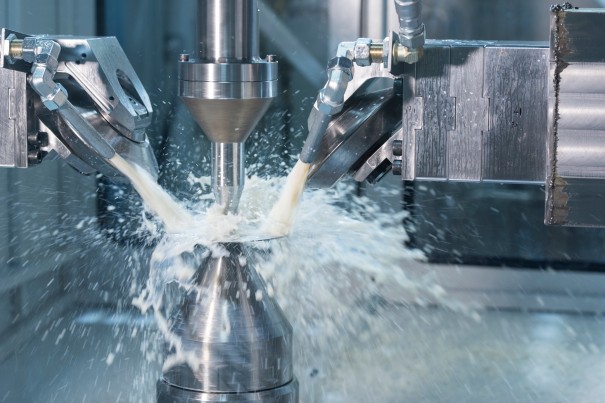
Silicate deposits on weld seams can be significantly reduced in the future thanks to an improved welding process for metal active gas welding (MAG), that we have developed together with our customer KIRCHHOFF Automotive, and an optimized pickling process.
Solutions-oriented processing
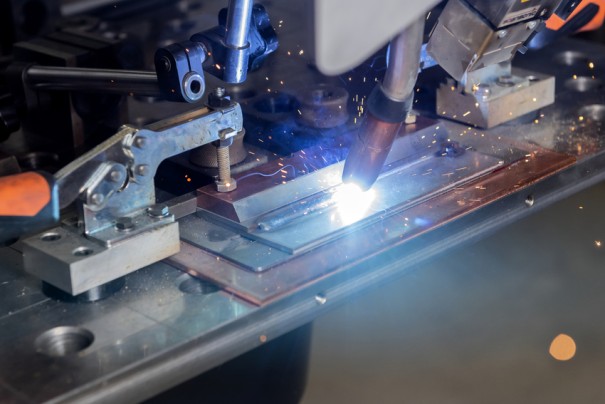
Silicate deposits on weld seams can be significantly reduced in the future thanks to an improved welding process for metal active gas welding (MAG), that we have developed together with our customer KIRCHHOFF Automotive, and an optimized pickling process.
Projects
Trends in the steel industry
Our innovative steels and surfaces and state-of-the-art production processes set clear trends in different industries.
With InCar® plus, we offer more than 40 innovative solutions for automotive efficiency and set benchmarks for lightweight construction, electrification and energy efficiency as well as safety and comfort.
selectrify® offers steel solutions for cost-efficient and safe e-mobility. From the vehicle structure through robust and safe battery housings down to electrical steel for highly efficient electric motors - selectrify® demonstrates the enormous potential of innovative steel solutions for electric vehicles.
Cooperations
Innovation needs cooperation
For the transformation to a climate-neutral industrial value chain to succeed, various product and process innovations must be interlinked. thyssenkrupp Steel relies on a dense innovation network of internal and external experts. In particular, this includes cooperation with universities, institutes and industrial partners. By involving our customers in development partnerships at an early stage, we also ensure that key requirements are taken into account and that new products and processes are smoothly integrated into the existing processes of steel processing companies.
Functional area
Thinking ahead about material trends
In the Innovation functional area, five specialist departments work across teams to develop and secure competitive solutions for the steel market.
Development and Market Launch
The department takes inspiration from the market, defines customer-specific solutions and develops them to market maturity. The introduction of new materials into internal and external production processes is also part of the product developers' remit. Against this backdrop, the teams are set up on a project-specific basis according to the skills required in each case and managed by a dual technical and commercial management team.
Contakt:
Dr. Hans-Peter Schmitz, Development and Market Launch,
[email protected]
Application Technology
Application technology characterizes new products and surfaces by examining and describing their behaviour in detail in the various processing stages. The department also works directly for customers, approves materials and tests various application scenarios. Basic projects for market launch are also carried out. The aim is to identify material concepts that can be optimally integrated into customer-specific processes.
Contakt:
Application Technology and Pilot Plants,
[email protected]
Materials Testing
With the help of various testing facilities, employees determine mechanical and technological parameters, identify microstructures and analyze surface coatings - for thyssenkrupp Steel and as an external service. Accredited release tests are also carried out around the clock for all coils produced - country-specific in accordance with the applicable test standards. Even very specific questions about the properties of steels are in the best hands with the highly specialized materials testers and material scientists.
Contakt:
Jörg Wehrstein, Materials Testing,
[email protected]
Chemical Laboratories
All substances and materials that thyssenkrupp Steel purchases, processes and produces pass through the testing processes of the chemical laboratories: Raw materials, products in various stages of production, by-products and residual materials, but also waste water and waste gases. Accordingly, the team uses a variety of analytical testing methods, including automated laboratories, innovative rapid tests and mobile analysis methods. Artificial intelligence is also increasingly being used. All services are also available as a service.
Contakt:
Dr. Eckhard Pappert, Chemical Laboratories,
[email protected]
IP Management
The IP Management department supports patent processes - from registration to the enforcement of license rights. It also keeps an eye on market trends and new developments and supports the innovation teams in the development of patent ideas. regularly guide our technical experts in developing patent ideas. As this requires a great deal of detailed knowledge, the team draws on a range of specialist expertise.
Contakt:
Christine Groth, IP Management,
[email protected]